Automated Guided Vehicles/Autonomous Mobile Robot (AGV/AMR)
Traditional manual material handling is expensive and requires extensive resources. In some instances, it can even be dangerous – a state of affairs that has helped propel a steady shift to more automated facilities. For all of the above reasons, Automated Guided Vehicles (AGVs) and Autonomous Mobile Robots (AMRs) are rapidly becoming a necessity for manufacturing, warehousing, and logistics facilities.
For industrial applications, these types of automated systems can decrease operational costs, increase safety, offer a competitive advantage and address the growing complexities of the supply chain. Moreover, with AGVs/AMRs taking on the dangerous, repetitive tasks, manufacturers can assign human resources to higher value-add tasks while simultaneously achieving new safety, productivity and cost-saving goals.
RTI works with the leading AGV/AMR manufacturers to deliver next-generation AGV/AMR systems that are capable of integrating the following functionalities:
- Advanced robotics, sensors and instrumentation
- Autonomous operations
- Teleoperations
- Fleet management
- Dynamic route management
- Data fusion, analytics and integration across devices and ecosystems
RTI Connext is a software connectivity framework
Connext enables interoperable, scalable and secure AGV/AMR platforms in mixed vendor environments. The high-level benefits of Connext for industrial automated applications include:
-
Reduced Cost and Accelerated Time-to-Market
Connext enables applications to be independent of the underlying network topology, allowing greater flexibility for deployment. Connext also fast-tracks integration with multi-vendor systems by eliminating the need for custom development. These factors can help significantly reduce costs and accelerate time-to-market for AGV/AMR manufacturers.
-
Security
Connext delivers fine-grained security that works over any network transport. Developers can authorize and grant access control – or restrict users – based on specific attributes such as role, data topic or action requested. These settings can be used to optimize security for heterogeneous systems that include components from multiple vendors.
-
Scalability
Connext enables logistics robots to share large amounts of data with differing data flows that originate from different data sources like cameras, lidars, positioning sensors and line sensors. The Connext databus handles data in motion, operating as a shared global space where data is continuously flowing between publishers and their matched subscribers, scalable to hundreds, thousands or more endpoints, thus eliminating single points of failure.
-
Interoperability
Connext is integrated with most industry standards, including ROS 2, OPC UA, DDS and TSN, enabling developers to use familiar platforms. Based on the Data Distribution Service (DDS™) standard, Connext communicates over the wire using the formal Real-time Publish-Subscribe (RTPS) protocol, an international standard managed by the Object Management Group® (OMG®).
-
Summary
Connext delivers a data-centric and future-proof architecture that can meet the fault tolerant, scalable, low latency, reliable and resilient, safety and security needs of AGV/AMR OEMs, as well as facilitate future innovation.
Looking for additional information?
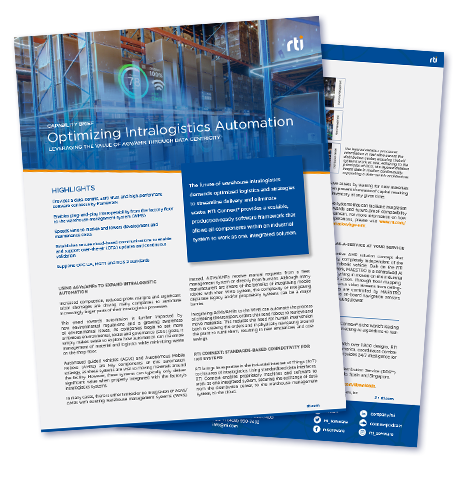
Optimizing Intralogistics Automation Capability Brief
Exploring the requirements for meeting the demands of the future of warehouse intralogistics, today.