3 min read
The RTI Military Avionics Blog Series Part 1: The Importance of Open Standards
Chip Downing
:
June 23, 2022
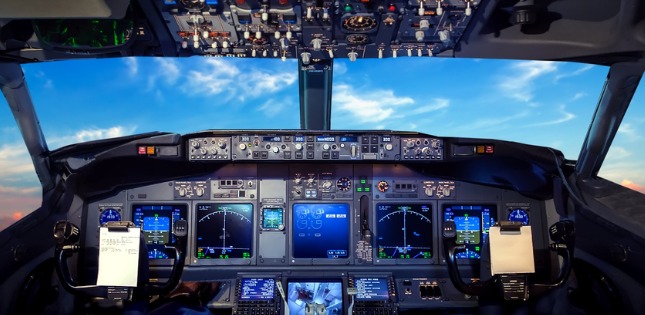
Part 1 of the RTI Military Avionics Blog Series
How important are open standards for the development of commercial aircraft? One way to illustrate the answer is this simple fact: One blog alone is not enough to capture it.
So, to do justice to this multifaceted topic, this blog is simply part one of an ongoing series. Our goal? To illustrate why adopting open standards is vital for success in today’s global commercial and military aerospace industries. We are going to explore how open avionics standards, most from the commercial avionics industry, can be applied to the development of military aircraft, driving increasing levels of efficiency and accelerated rates of deployment as a result.
Let’s start with the understatement of the century: the cost and risk of building commercial aircraft is immense. To help bring greater order to the process, the global commercial aerospace industry created a rich set of standards, many controlled by the ARINC standards body, that cover nearly all aspects of building and operating commercial airliners. These standards in turn create a stable market for aerospace systems developers which immediately creates opportunities within the supply chain for greater investment and innovation.
One of these standards, ARINC 653, has saved the industry billions of dollars, and continues to save manufacturers more money every day. ARINC 653 spearheaded the industry migration from federated, or standalone, avionics systems to Integrated Modular Avionics (IMA) platforms. The evolution from hardware-centric to software-centric systems accelerated this transition, due to significant reductions in Size, Weight, and Power and related Costs (SWAP-C).
![]()
|
Figure 1. Federated avionics architecture. |
Federated compute architectures typically include an enclosure, redundant power supplies, redundant compute systems with RTOSs, board support packages (BSPs), network/connectivity software and finally federated software applications. This is great for maintenance -- one simply swaps out the federated box and replaces it with another. But as the volume of software applications increases on an aircraft, basing things on individual federated systems becomes untenable due to SWAP-C concerns.
Enter the ARINC 653 IMA platform. This is a singular platform, typically with triple redundant processors, power supplies and network connections. There is only one Real-Time Operating System (RTOS). And most of the application software on the aircraft is hosted on a time-and-space partitioned environment with other application software (there still may be a few federated systems on the aircraft). But this environment removes the requirements for every software component to have its own heavyweight hardware, RTOS, power and network infrastructure: Only application software is delivered to this ARINC 653 party.
In modern software-centric aircraft, this IMA architecture can save over one thousand pounds, opening up the opportunity to fly further, as well as fly more passengers, cargo or fuel, thanks to these SWAP-C savings. And today, IMA systems are proven in use. There are now over one hundred different commercial and military airframe types that employ an IMA architecture, including aircraft by Airbus, Boeing, KAI, KHI, IHI, Leonardo, Lockheed Martin Sikorsky, Mitsubishi, and Northrop Grumman.
Figure 2. Notional diagram of transitioning federated hardware-centric platforms into an IMA system.
Defining Supplier Roles: RTCA DO-297
In the commercial avionics industry, a business process was developed, RTCA DO-297, “Integrated Modular Avionics (IMA) Development Guidance and Certification Considerations”, that defines three supplier roles that contribute hardware and software on a shared IMA platform to manage the complexity and cost of merging and integrating mixed safety level software components on a flight-critical platform.
The overarching goal of DO-297 is that Application Suppliers should be able to independently work on their specific deliverable using only the IMA platform library supplied by the Platform Supplier, and not be exposed to unexpected responsibilities, cost and risk. DO-297 provides clear guidance and separation of all IMA suppliers and subcontractors, allowing them to focus on delivering their aspect of the system, including the relevant RTCA DO-178C avionics safety certification artifacts.
The three DO-297 supplier roles are:
- IMA Platform Supplier: Prepares the hardware compute environment, OS/RTOS, board support package (BSP), aircraft platform capabilities and the communication infrastructure for applications, as well as all related safety and security certification evidence.
- Multiple IMA Application Suppliers: Provide hosted functions, with appropriate certification evidence, which execute protected ARINC 653 partitions.
- IMA System Integrator: Ties together this environment on a given airframe platform and achieves aircraft platform airworthiness.
Figure 3. RTCA DO-297 Supplier Roles
This role separation on IMA platforms not only saves on hardware, but also saves on software development tool costs. Only the IMA Platform Supplier needs to procure a full array of tooling to create an ARINC 653 RTOS, board support packages, network drivers and more. The IMA software applications, many having different levels of safety criticality, only need to have enough tooling to compile/debug their software, create certification evidence, and link it to the IMA Platform binary. In the spirit of ARINC 653 platform consistency and cost containment, this IMA Platform binary is provided at no cost to all suppliers, driving both uniformity and efficiency throughout the DO-297 supply chain.
ARINC 653 and RTCA DO-297 provide a fantastic example of how using open industry standards reduces supplier cost and risk while driving supply chain efficiencies throughout the aircraft, both during development and flight operations. The billions of dollars saved just by using these two standards allow commercial and military aircraft systems manufacturers to focus on production quality, airworthiness and operational efficiency, while enabling the rapid and reliable transition to software-defined aircraft.
Join us in two weeks for Part 2 in the RTI Military Avionics Blog Series. In the meantime, we invite you to visit rti.com to learn more about the ways RTI software and industry experience helps aircraft manufacturers succeed.
About the author
Chip Downing is Senior Market Development Director, Aerospace & Defense, Real-Time Innovations, Inc.
Chair, FACE Business Working Group Outreach Subcommittee
Posts by Tag
- Developers/Engineer (178)
- Technology (78)
- Connext DDS Suite (77)
- News & Events (74)
- 2020 (54)
- Standards & Consortia (51)
- Aerospace & Defense (49)
- Automotive (36)
- 2023 (34)
- 2022 (29)
- IIoT (27)
- Leadership (24)
- 2024 (22)
- Cybersecurity (20)
- Healthcare (20)
- 2021 (19)
- Connectivity Technology (17)
- Military Avionics (15)
- Culture & Careers (14)
- 2025 (13)
- FACE (13)
- Connext DDS Pro (10)
- JADC2 (10)
- ROS 2 (10)
- Connext DDS Tools (7)
- Connext DDS Micro (6)
- Databus (6)
- Transportation (5)
- Case + Code (4)
- Connext DDS (4)
- Connext DDS Cert (4)
- Energy Systems (4)
- FACE Technical Standard (4)
- Oil & Gas (3)
- RTI Labs (3)
- Research (3)
- Robotics (3)
- #A&D (2)
- Connext Conference (2)
- Edge Computing (2)
- MDO (2)
- MS&T (2)
- TSN (2)
- ABMS (1)
- AI (1)
- C4ISR (1)
- DOD (1)
- ISO 26262 (1)
- L3Harris (1)
- LabView (1)
- MOSA (1)
- MathWorks (1)
- National Instruments (1)
- Simulation (1)
- Tech Talks (1)
- UAM (1)
- Videos (1)
- eVTOL (1)